MasterMatrix LF
compensates for up to
50-70Kg of fines in concrete
When fines are not enough
MasterMatrix LF improves the stability and homogeneity of concrete whenever you are facing a shortage in fines or binder paste (LF stands for low-fines).
A dose of only 1 to 1.5 Kg of MasterMatrix LF can compensate for up to 70Kg of fines (particles with a diameter < 250 μ) per m3 of concrete or alternatively for up to 40 liters of paste.
Why develop a solution for the shortage of fines in concrete?
Concrete needs a certain amount of fines to be “good”, homogeneous, easy to pour, pump and finish. When the fines are not enough for your production of concrete, you will meet problems of concrete stability and homogeneity, therefore of pumpability and placeability.
Nowadays, the scarce availability of fly ash and slag pose a serious concern. In many cases where fines are scarse or poor, the ready-mix producer can only increase the dosage of cement as corrective action, but this brings about an increase of CO2 emissions and increases costs.
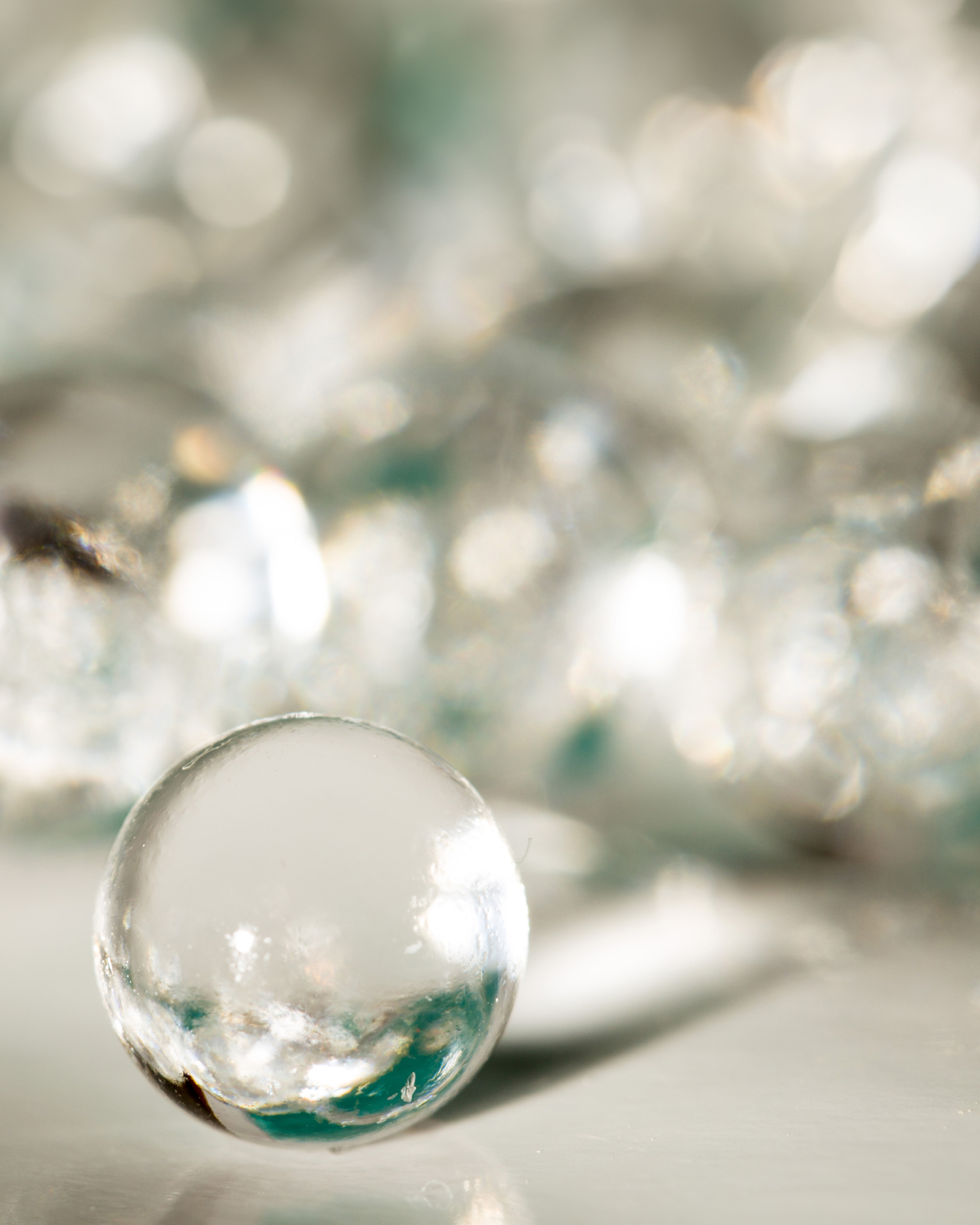
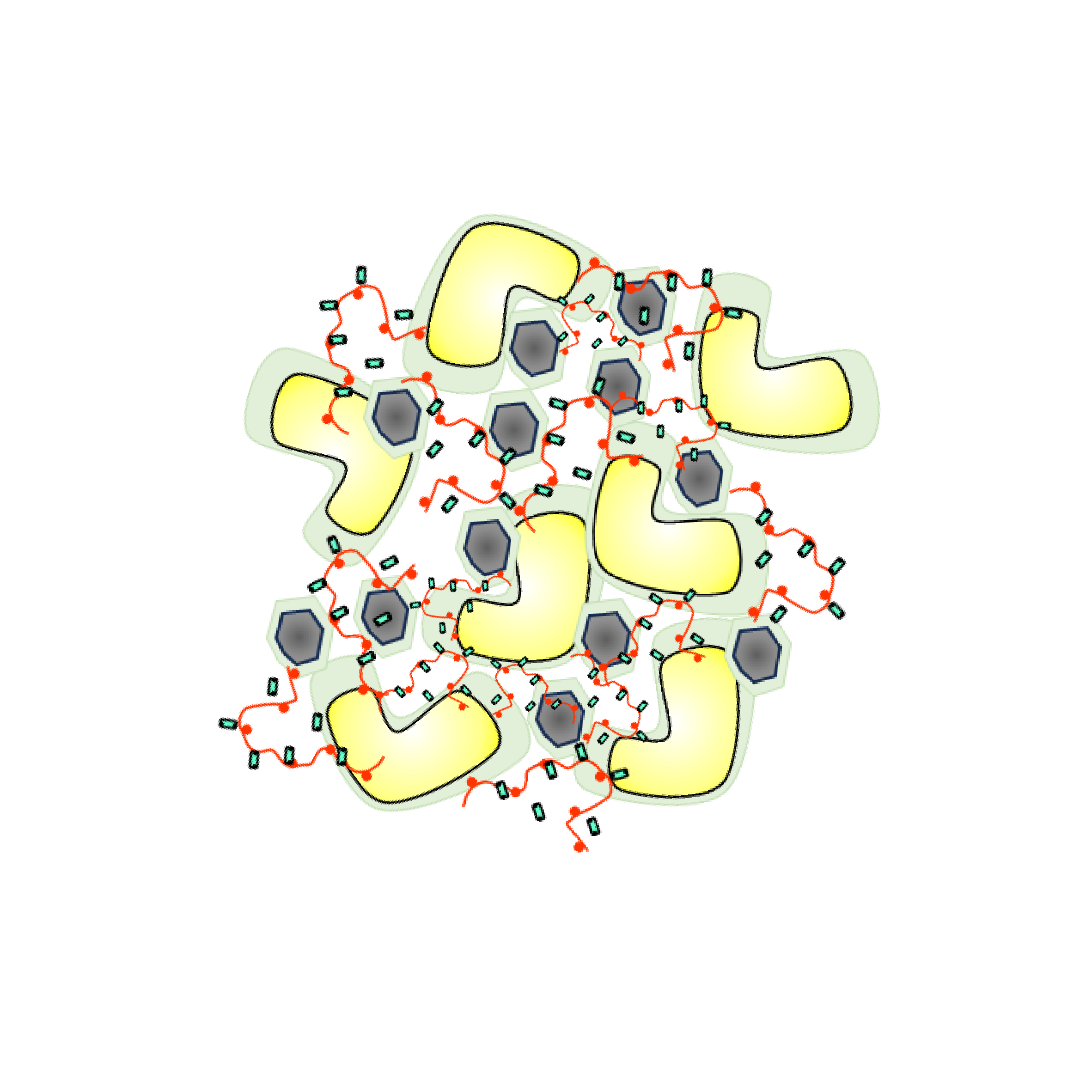
Applications
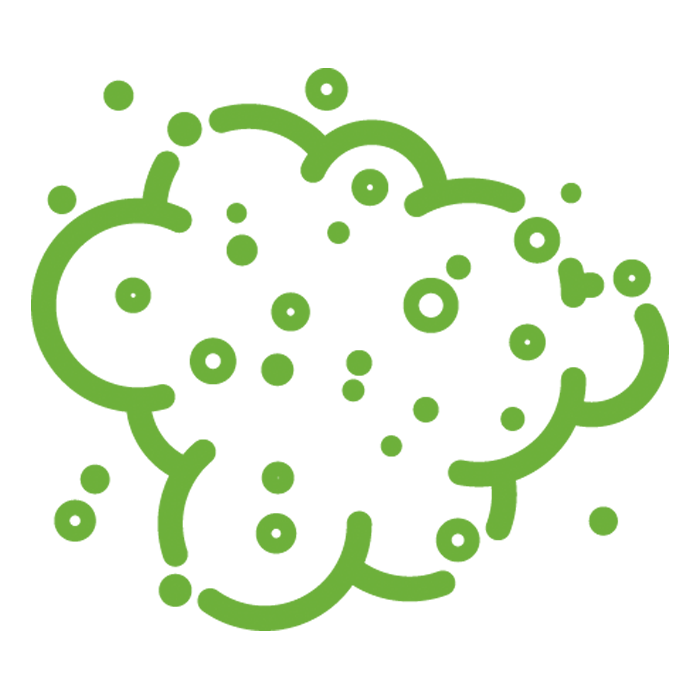
Lack of fly ash
You, ready-mix concrete producer, used to have fly ash, but nowadays this element is not available anymore. To compensate for the lack of fly ash, you can use more expensive limestone filler or, even worse, increase the dosage of cement. By using MasterMatrix LF, you can avoid this.
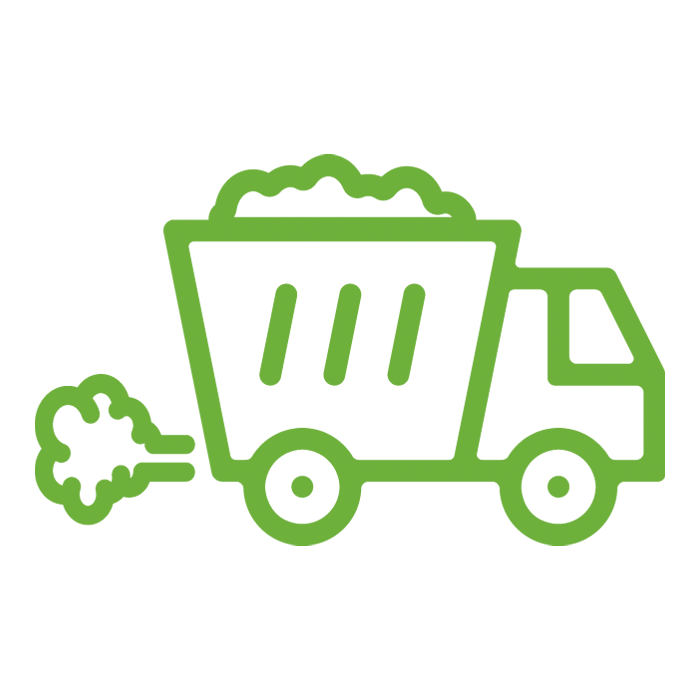
Sand lacking fines
The sand from the quarry closest to your plant is lacking fines, either because it is intrinsically poor or because it has been deeply washed. Today, you are obliged to use a “corrective sand”, that is coming from further away, which means higher transportation distances, more CO2 emissions, higher costs. You can avoid this, by using MasterMatrix LF.
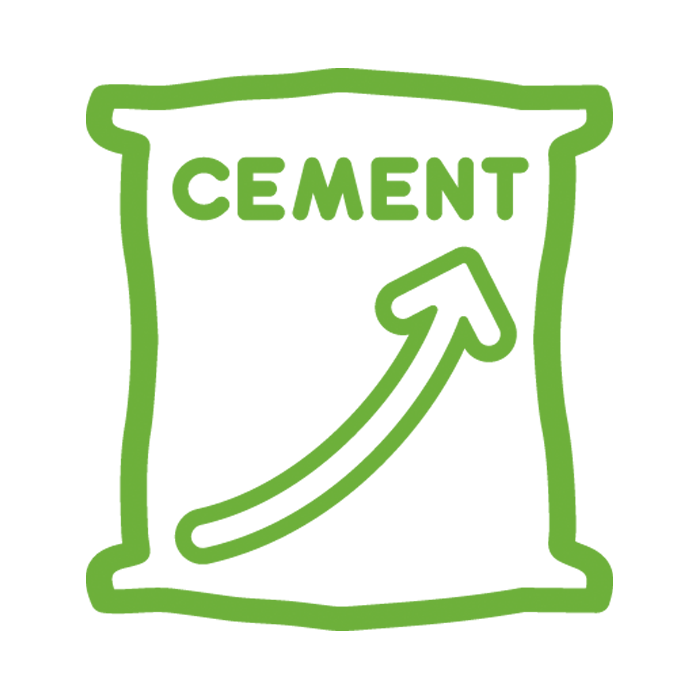
Stable SCC
In case of scarcity of fines (fly ash or limestone filler) or if you do not have a silo to allocate them, and you want to produce Self Compacting Concrete, you have to overdose the cement. This can be avoided with MasterMatrix LF.
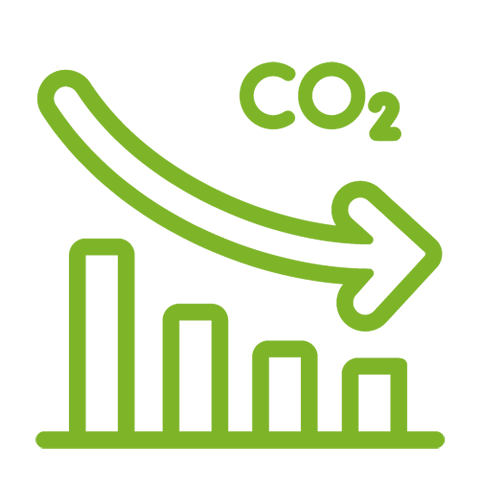
Low-clinker cements
Increasing use of low-clinker cements driven by sustainability goals prompts reduced water content, impacting paste volume and thus concrete handling properties. Again, MasterMatrix LF can make the difference.
Application examples
Scenario 1
In this first case, limestone filler was replaced by the corresponding volume of sand. Then the compositions of the Reference Concrete and the Low Fines Concrete - with MasterMatrix LF added - have been compared and the tests carried out on the concrete mixes in their fresh state.
Scenario 2
We have simulated the situation where the concrete producer increases the proportion of crushed sand because of a scarcity of natural sand, which is one of the typical cases where the stability of the concrete is reduced. Again, tests were carried out on the concrete mixes in their fresh state.
Want to deepen the topic and discover the tests results?
Read the article from Nicoletta Zeminian, Customer Segment Manager Ready-Mix & Site-Mix Europe and Sandro Moro, Concrete Technology and Materials Innovation Manager at Master Builders Solutions.
Reference concrete containing 235 Kg of cement and 75 Kg of fly ash
It’s a very good quality concrete, but nowadays it’s hard to find fly ash
Low fines concrete containing 250 Kg of cement
It is as good as the reference concrete thanks to the addition of MasterMatrix LF that compensates for the 60 Kg of missing fines
Decoding how MasterMatrix LF works
MasterMatrix LF operates through two core mechanisms, synergistically combined to enhance concrete performance:
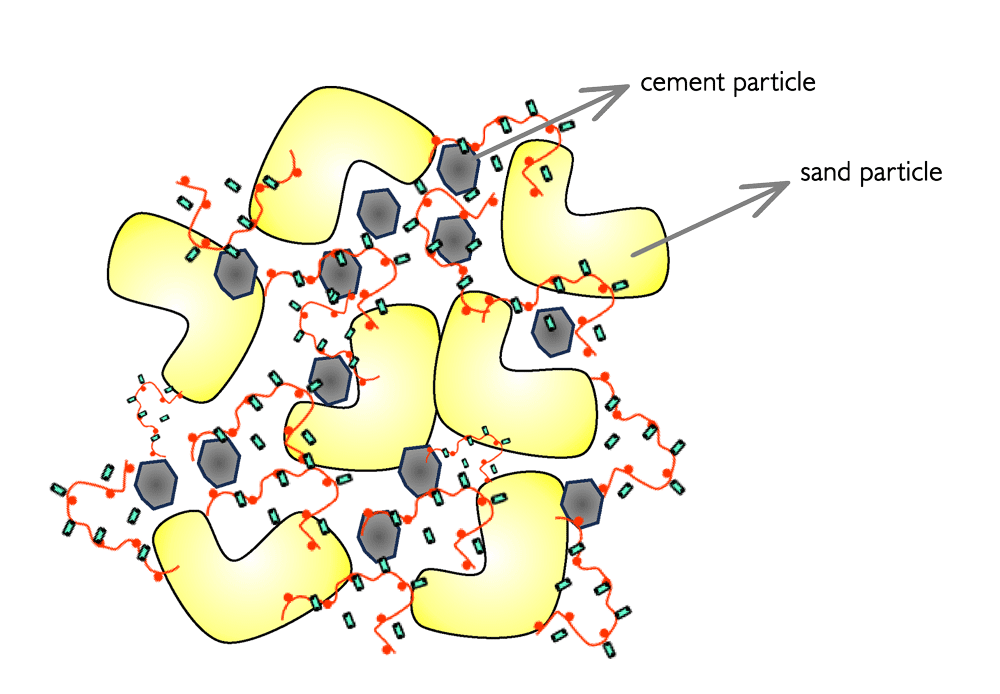
Viscosity Optimization
Engineered polymers in MasterMatrix LF delicately adjust viscosity for stability and uniformity. Unlike conventional agents, it exhibits shear-thinning behavior, ensuring stability when stationary and easy flow upon motion. Forming a cohesive network among particles, it dynamically adjusts viscosity for consistent rheology.
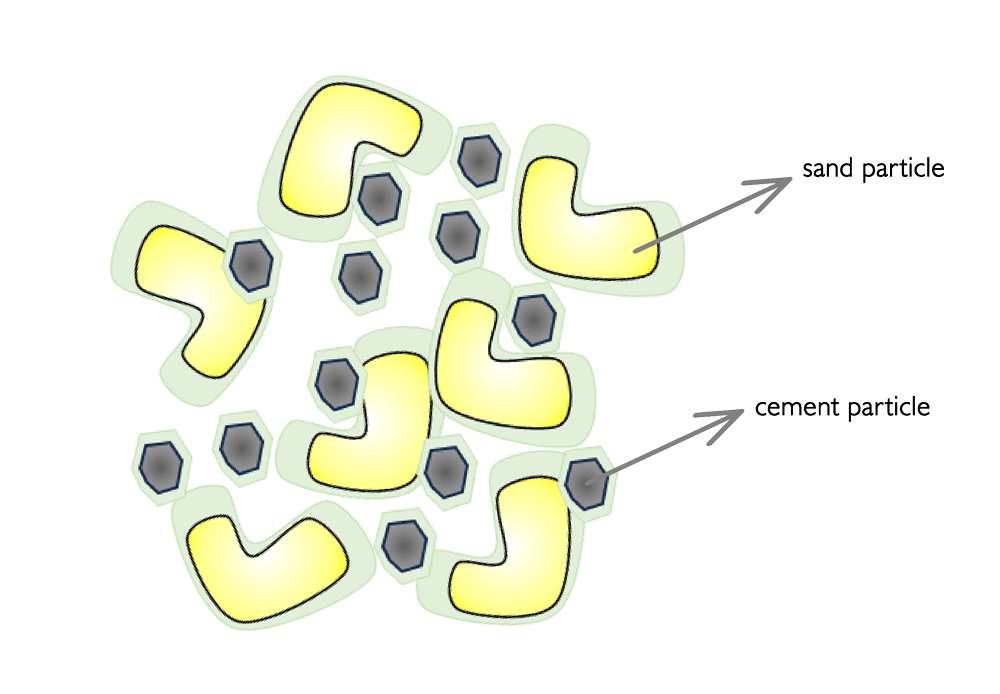
Friction Reduction
Acting akin to mechanical bearings, MasterMatrix LF envelops solid particles within the concrete mix, reducing inter-particle friction and dissipating energy. This tribological effect enhances lubrication, further enhancing concrete fluidity and workability.
ECO2NOW™ Concrete Calculator
Rising energy and raw material prices and the need to switch to more sustainable production methods are currently the biggest challenges for the construction industry. The increasing cost pressure makes sustainable action more difficult. However, sustainability and economic efficiency are not mutually exclusive and go hand in hand.
Do you also want to make a sustainable contribution and optimize your concrete mix in terms of CO2 and costs? Don't loose time and set up a meeting with your local Master Builders Solutions expert today.
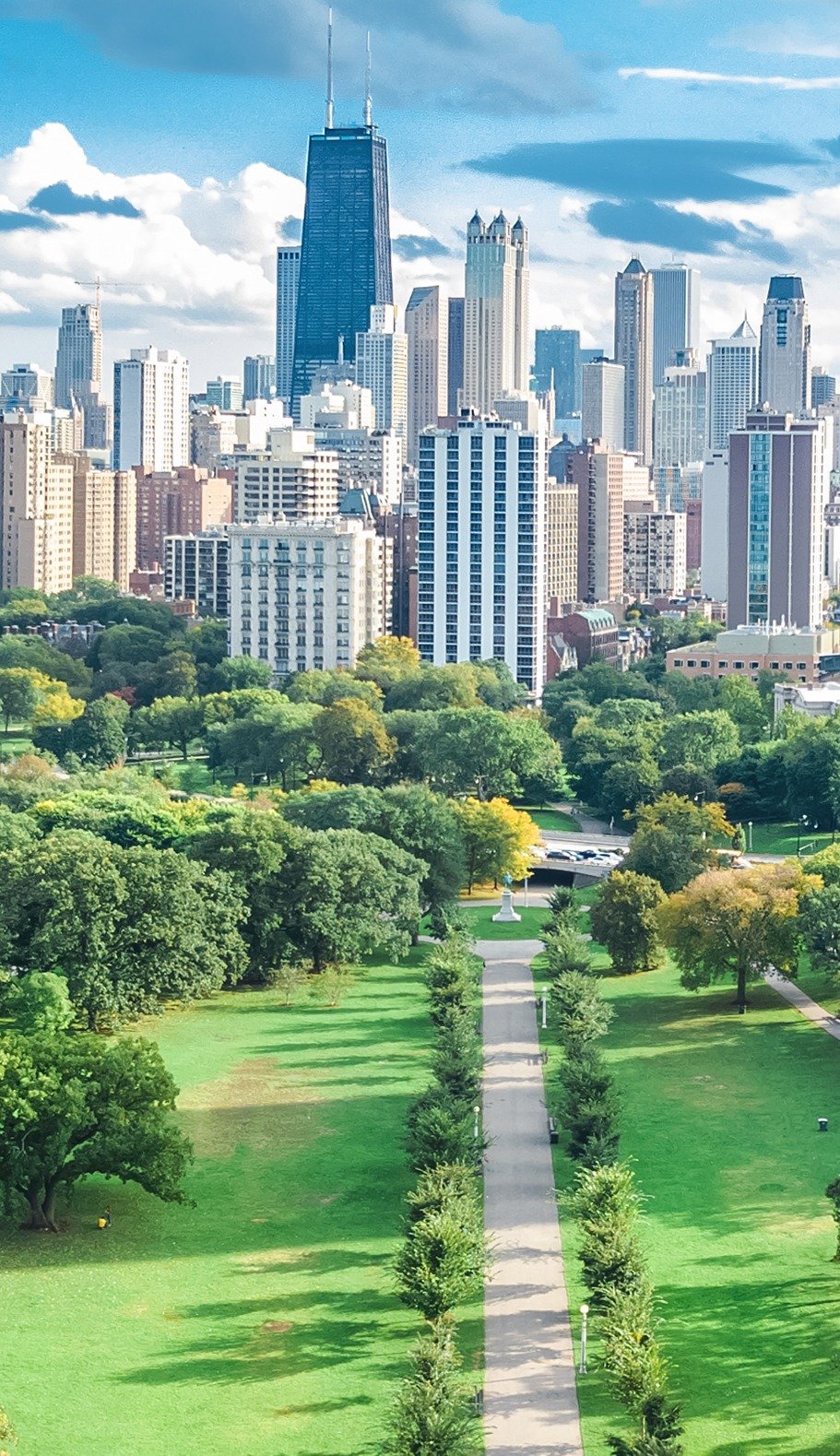
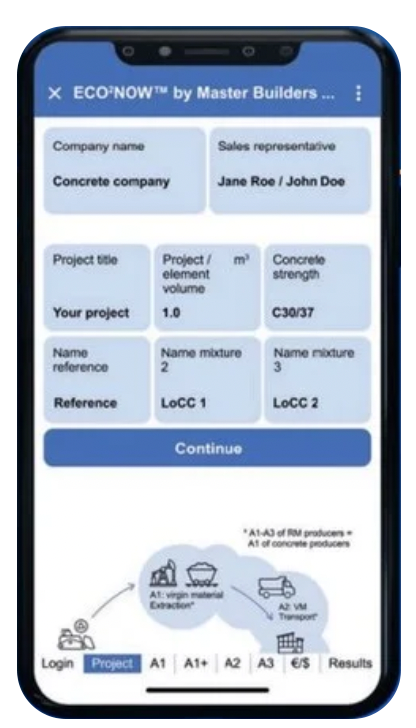